Bài viết trước, chúng tôi có chia sẻ về Lean Manufacturing là gì? Tại sao khi nhắc tới Lean mọi người đều liên tưởng tới Toyota?. Trong bài viết này sẽ là những ví dụ điển hình về các công ty áp dụng Lean Manufacturing thành công.
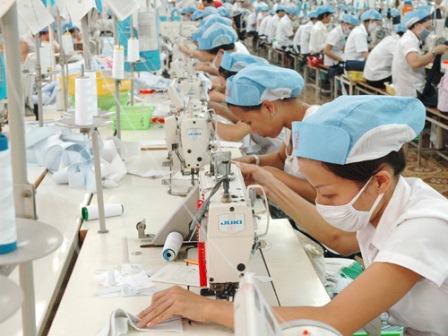
Lean là phương pháp sản xuất tinh gọn được áp dụng rộng rãi trên toàn thế giới. Với mục đích chung là tinh gọn sản xuất.
- Giảm chi phí
- Loại bỏ lãng phí
- Tăng năng suất, sản lượng
- Rút ngắn thời gian sản xuất
- Tăng hiệu quả kinh doanh.
Mỗi doanh nghiệp có cách quản lý sản xuất khác nhau, quy trình khác nhau. Vì thế việc sao chép nguyên bản phương pháp quản lý sản xuất của một công ty khác là điều không nên. Các nhà kinh doanh với đầu óc nhanh nhạy, chọn lọc các phương thức phù hợp để triển khai cho doanh nghiệp mình, tự tìm hướng đi riêng sẽ có khả năng thành công cao hơn số còn lại.
Đương nhiên sẽ có các nguyên tắc chung cho các công ty sản xuất. Mọi người có thể coi đó là xương sống. Hãy tham khảo 1 vài công ty hiện đã, đang và sẽ tiếp tục triển khai các quy trình tinh gọn và cách họ thực hiện chúng.
Mục lục chính
Các công ty áp dụng Lean Manufacturing thành công tại Việt Nam
Thực tế ngành công nghiệp sản xuất tại Việt Nam đã có nhiều công ty ứng dụng Lean và đạt được những thành công vượt trội. Trong quá trình triển khai gặp không ít vấn đề, trục trặc. Có thể kể tới một số doanh nghiệp lớn như dưới đây.
Các công ty dệt may Việt Nam
Nổi trội trong số các doanh nghiệp ứng dụng hiệu quả có thể kể tới các doanh nghiệp trong ngành Dệt may. Năng suất tăng, tỷ lệ hàng lỗi giảm, thời gian làm việc rút ngắn lại, chi phí sản xuất giảm, thu nhập người lao động tăng,… Đó là những gì mà các doanh nghiệp dệt may tổng kết được sau khi triển khai thành công phương pháp sản xuất tinh gọn.
Sản xuất tinh gọn – Lean được giới thiệu đến các công ty Dệt may Việt Nam bắt đầu từ những năm 2006. Một số công ty sau khi áp dụng Lean đã đạt được các kết quả như sau:
Tổng công ty May 10
Biết tới Lean từ năm 2007, nhưng phải vài năm sau May 10 mới triển khai áp dụng. Thành công tới với May 10 khi tổng kết kết quả hoạt động sản xuất kinh doanh: năng suất lao động của đơn vị tăng 52%, tỷ lệ hàng lỗi giảm tới 8%, giảm chi phí sản xuất từ 5-10%/năm. Thêm vào đó giờ làm được giảm bớt 1 giờ/ ngày, không cần tăng ca kíp mà thu nhập lao động cũng tăng trung bình 10%.
Tổng công Cổ phần Dệt may Hòa Thọ
Sau khi tiến hành áp dụng phương pháp sản xuất tinh gọn tại công ty, hiệu quả mang lại cho Dệt may Hòa Thọ trước hết phải kể tới hiệu quả sử dụng mặt bằng nhà xưởng. Diện tích sử dụng được thu gọn, hàng hóa sắp xếp khoa học, giảm thiểu thời gian lãng phí khi di chuyển trong nhà xưởng.
Trước khi áp dụng Lean, trên dây chuyền sản xuất thường bị tồn động khi chuyển công đoạn. Lean đã giúp giảm hàng tồn trên dây chuyền từ 30 xuống còn 3 sản phẩm. Tốc độ sản xuất đã tăng lên, chuyên nghiệp hơn và hiệu quả hơn. Từ đó giúp giảm hàng lỗi từ 20% xuống còn 8%.
Tư tưởng người lao động được ổn định, cầu tiến, đặc biệt không cần làm thêm giờ mà thu nhập vẫn tăng.

Tổng công ty May Việt Tiến
Lần đầu áp dụng Lean thất bại năm 2007, 1 năm sau, ban lãnh đạo của Việt Tiến quyết tâm triển khai lại sản xuất tinh gọn để thúc đẩy phát triển.
Thành công đã tới với Việt Tiến. Năng suất lao động tăng bình quân 20%, giảm hàng lỗi, tiết kiệm chi phí để đầu tư áp dụng công nghệ sản xuất mới. Ngoài ra, Việt Tiến cũng tiết kiệm mặt bằng để mở rộng sản xuất, mà không cần xây dựng thêm nhà xưởng.
>>> Xem thêm: Các ý tưởng cải tiến trong thời kỳ sản xuất để vượt qua thời kỳ Covid-19
Tổng Công ty May Nhà Bè – CTCP (NBC)
Áp dụng Lean từ năm 2013, từ đó trở đi, NBC liên tục thực hiện các cải tiến sản xuất. Đầu tiên là triển khai đồng loạt Lean cho một loại sản phẩm. Sau đso tiếp tục triển khai cho cả tổ sản xuất. Kết quả áp dụng Lean thu về cho NBC là năng suất toàn hệ thống tăng hơn 20%. Các dây chuyền sản xuất ổn định, kiểm soát theo từng giờ sản xuất.
Cũng giống như các công ty may phía trên, giờ làm việc của người lao động cũng giảm 1h/ngày, thêm 1 ngày nghỉ cho nhân viên. Thậm chí các ca kíp làm việc cũng bỏ hoàn toàn. Hàng lỗi giảm từ 20% còn 3%.
Tại sao lại có sự cải thiện lớn như thế sau khi triển khai Lean Manufacturing?
Cải tiến sản xuất cần thực hiện liên tục, đồng bộ, áp dụng theo các quy chuẩn đã có để đạt được hiệu quả triệt để.
So sánh với các dây chuyền sản xuất truyền thống ta sẽ thấy sự khác biệt.
- Các công nhân làm việc tùy hứng
- Lựa chọn vị ngồi tùy thích
- Khoảng cách giữa các công đoạn xa nhau
- Lương thưởng được trả theo số lượng sản phẩm, nhưng lại không tính tới độ khó của công đoạn. Gây ra nội bộ lục đục.
Lean đã cải tiến tất cả những điều trên.
- Các nhân viên thực hiện đồng bộ công việc
- Dây chuyền sắp xếp hợp lý, giảm lãng phí di chuyển qua lại trong nhà máy.
- Tính đoàn kết của các bộ phận tăng lên
- Dây chuyền sản xuất liên tục, năng suất tăng,…
- Lương công nhân trả theo thực lực, tính theo sản lượng của cả dây chuyền sản xuất.
- Chế độ đãi ngộ tốt hơn: hệ số lương theo thâm niên, phân chia cấp bậc phù hợp để mọi người hỗ trợ nhau trong cùng 1 dây chuyền.
- Nhiều lợi ích khác được kéo theo khiến hoạt động của doanh nghiệp tốt lên.
Một kinh nghiệm có thể rút ra là việc triển khai Lean tại các đơn vị, điều quan trọng nên làm là cần tập trung vào nguồn nhân lực đầu vào để cải thiện hệ thống. Xây dựng đội ngũ trẻ có trình độ và tâm huyết để đạt được những mục tiêu ngắn hạn và dài hạn cho đơn vị.
>> Xem thêm: Cải tiến công đoạn sản xuất là gì? Ví dụ thực tế về cải tiến sản xuất trong các doanh nghiệp
Các vấn đề thường gặp khi áp dụng phương pháp tinh gọn sản xuất tại Việt Nam
- Người Việt nam có khả năng cải tiến tốt, nhưng rất khó để duy trì việc triển khai cải tiến liên tục về lâu dài. Khi mới có kết quả đã tự cho là thành công, không tiếp tục duy trì các hoạt động cải tiến.
- Khi thích thì làm rất nhanh, nhưng ẩu.
- Chỉ nhìn thấy cây mà không nhìn thấy rừng. Chỉ thấy bộ phận mà không thấy toàn thể.
- Tinh thần giúp đỡ nhau tốt, nhưng tinh thần trách nhiệm thì không cao.
- Khả năng ứng phó với các bất thường rất tốt, nhưng khả năng làm cho bất thường đó không xảy ra nữa rất kém.
Các công ty áp dụng Lean Manufacturing điển hình trên thế giới
TOYOTA
Phương pháp sản xuất Lean được cả thế giới biết tới là nhờ công của Toyota. Sản xuất tinh gọn được Toyota nghiên cứu và phát triển, tổng hợp thành Hệ thống sản xuất Toyota (TPS).
Toyota không chỉ loại bỏ hết các lãng phí mà còn đưa ra các kỹ thuật cần thiết để giảm thiểu các sản phẩm lỗi tới tay khách hàng.
Toyota làm việc với hai quy trình chính cho phép đạt được những mục tiêu này.
- Đầu tiên là một quy trình có tên Jidoka, tạm dịch là “tự động hóa sản xuất có sự trợ giúp của con người”. Điều này có nghĩa là mặc dù một số quy trình của công việc được tự động hóa, nhưng con người vẫn liên tục kiểm tra chất lượng của sản phẩm. Các chương trình được tích hợp để máy móc tự phát hiện sự cố, đưa ra cảnh báo và dừng hoạt động để đảm bảo an toàn. (Andon System)
- Phần thứ hai được gọi là mô hình Just In Time hoặc JIT. Điều này đảm bảo rằng bước tiếp theo của quy trình chỉ được bắt đầu sau khi giai đoạn trước đó được hoàn thành. Bằng cách này, nếu có sai sót trong dây chuyền lắp ráp, nó ngay lập tức bị loại bỏ. Đảm bảo không có thao tác lãng phí nào cho việc sản xuất sản phẩm lỗi.
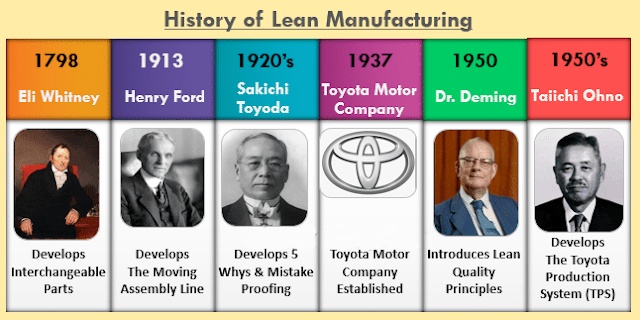
INTEL
Nổi tiếng với bộ vi xử lý máy tính, Intel đã áp dụng các kỹ thuật sản xuất tinh gọn để cung cấp sản phẩm chất lượng cao hơn cho một ngành công nghiệp không được phép có lỗi.
Sản xuất tinh gọn đã giúp INTEL giảm thời gian sản xuất 1 vi mạch từ ba tháng xuống còn 10 ngày. Với các mặt hàng cần chính xác và kỹ thuật, Intel nhanh chóng nhận ra rằng sản xuất với số lượng cao hơn mà chất lượng thấp hơn không phải là cách để cải thiện lợi nhuận và tăng sự hài lòng của khách hàng.
Thay vào đó, Intel áp dụng các yếu tố kiểm soát chất lượng và phương pháp giảm thiểu lãng phí. Cả chất lượng và năng suất đều tăng cao.
Các ngành công nghệ là nơi mà Lean được phát huy tối đa. Với các sản phẩm luôn được thay đổi và nâng cấp thường xuyên.
JOHN DEERE
John Deere là công ty chuyên sản xuất xe đầu kéo. Họ cũng đã áp dụng sản xuất tinh gọn cho doanh nghiệp của họ. Nhiều cơ chế kiểm soát chất lượng của họ hoàn toàn tự động.
Kiếm soát từng bộ phận trong sản phẩm, số lượng các bộ phận được sản xuất có thể được kiểm tra trong thời gian ngắn hơn. Điều này có nghĩa là mỗi ngày có thể có nhiều sản phẩm được sản xuất hơn. Sản phẩm có thể được cung cấp cho người tiêu dùng với giá thấp hơn.
NIKE
Gã khổng lồ giày và quần áo nổi tiếng cũng đã áp dụng các kỹ thuật sản xuất tinh gọn. Giống như các doanh nghiệp khác, Nike nhận thấy ít lãng phí hơn và giá trị khách hàng cao hơn.
Nike cũng không ngờ tới những lợi ích các phương pháp Lean mang lại. Sản xuất tinh gọn đã được chứng minh là làm giảm tới 15% lượng lao động kém trong nhà máy sản xuất ở nước ngoài của NIKE.
Điều này chủ yếu là do sản xuất tinh gọn thanh lọc những người lao động có trình độ cao hơn so với các phương thức lao động trước đây. Nó mang lại giá trị quan trọng hơn cho một nhân viên và do đó giá trị cao hơn cho toàn công ty.
Bài học
Mục đích cuối cùng của các doanh nghiệp chính là lợi nhuận. Vậy làm thế nào để tăng lợi nhuận mà vẫn giữ nguyên giá bán?
Công thức chung của giá bán được tính như sau:
Giá bán = giá thành + lợi nhuận
Theo công thức trên, để tăng được lợi nhuận, thì giá bán phải tăng, trong trường hợp giá thành cố định.
Với Toyota, cũng là cách tính đó nhưng đứng trên phương diện có lợi cho khách hàng:
Lợi nhuận = giá bán – giá thành
Để tăng lợi nhuận, Toyota sẽ không tăng giá bán, mà tìm cách giảm giá thành tới mức tối thiểu. Sức cạnh tranh cũng từ đó tăng theo.
Để giảm giá thành cần nâng cao năng suất của:
- Lực lượng lao động (Tiết kiệm lao động vẫn đảm bảo năng suất)
- Nguyên vật liệu (Sử dụng đúng đủ nguyên liệu đầu vào, giảm lượng phế phẩm)
- Thiết bị sản xuất (Đầu tư thiết bị, máy móc phù hợp với nhu cầu thực tế, hiệu suất cao)
Đồng nghĩa với việc loại bỏ tất cả những lãng phí không cần thiết để tối ưu hóa hoạt động sản xuất.
Kết luận
Sản xuất tinh gọn là một quá trình mà nhiều doanh nghiệp sẽ tiếp tục áp dụng tốt trong tương lai. Bằng cách giảm thiểu lãng phí và tối đa hóa giá trị cho khách hàng, cả người tiêu dùng và công ty đều có thể hưởng lợi từ việc thực hiện nó. Hầu hết các công ty đã nhìn thấy lợi ích của hệ thống sản xuất tinh gọn. Và đã cố gắng triển khai hệ thống theo quy trình của riêng họ với nhiều cải tiến sáng tạo.
Nếu bài viết này chưa thỏa mãn điều bạn cần, bạn hãy đọc bài viết: Cải tiến trong sản xuất – các doanh nghiệp FDI đã thực hiện như thế nào?
CÔNG TY CỔ PHẦN NĂNG LỰC VIỆT
- Địa chỉ : Lô đất số B2-3-3b KCN Nam Thăng Long – P. Thụy Phương – Q. Bắc Từ Liêm – TP. Hà Nội.
- Tel: (+84)24.37805300 – Fax: (+84)24.37805301
- Hotline/Zalo: 0934 683 166
- Email: contact@vcc-group.vn